2 Apr '15
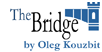
Oleg Kouzbit, Online News Managing Editor
Scientists from Kazan National Research Technological University, Tatarstan, have offered the nonmetallic minerals sector a new production technique. Microwaves are coming to replace electrical current and ignition used now in conventional toxic-hazardous methods. The researchers claim that the technology saves production costs, leaves little waste in the process compared to traditional blasting, and helps produce higher-quality material. It could also be very helpful for other purposes, such as housebreaking, slum clearance, or rock fragmentation on construction sites.
In a bid to improve the blasting method of producing nonmetallic minerals, Russian companies favorite for decades, the Tatarstan researchers have developed an innovative explosive detonation technique that uses radio-wave emission rather than conventional ignition or electrical current.
The developer
Kazan National Research Technological University (KNRTU) is one of the oldest higher educational institutions in the Mid-Volga area. Set up in 1890 as Kazan Industrial College, KNRTU has evolved into a university that ranks tenth out of Russias 159 technology universities. It runs 99 academic departments.
The university is a player in the innovation field in Tatarstan and Russia as a whole, collaborating with universities and businesses from more than 20 countries.
How the innovation works
With the new approach, a whole new set of opportunities may open up in production of basalt, granite, sand, clay and other well-known minerals widely used in construction for centuries. Ironically, current techniques to produce these materials, readily available in many areas across the planet, are still far from cost-effective.
In the KNRTU technology, special holes are bored in rock mass where ammonium nitrate is placed in a special explosive mixture. The holes are then thoroughly tamped with sand and polymers. When exposed to targeted microwave radiation, the explosive mixture blazes up, causing a sharp increase in pressure and subsequent cleavage of rock.
Emission power can be carefully controlled and an amount of explosives chosen to make sure the blast effectively splits the rock mass while keeping down dust formation and fragmented waste.
Alternatives: pros and cons
The technique is believed to bring about results similar in rock fragmentation power to what is known as air cushion, a traditional method that calls for the pumping of air inside rock strata through specially drilled holes, with rock mass then destroyed by overpressure. However, air cushion is much costlier, experts say.
Another alternative way of producing nonmetals is conventional blasting with electrical current or ignitionthe one that the Tatarstan innovation may come to replace. It is considered the cheapest as of today, and most widespread.
With this economical and widely used method, why bother with any improvement?
Theres a good reason for that, the Kazan researchers think. In an explosion, about 30% of rock turns into useless dust and the remaining 70% is shattered into cracked fragments of various size. It is a low-quality product that requires further on-the-spot processing, with a lot of unrecoverable waste to be simply thrown away. Most explosives used in standard blasting are toxic and hazardous to personnel.
Testing and proving
To see if their invention is really a cut above that old routine approach KNRTU put it to the test. Ammonium nitrate and diesel fuela mixture that is not explosive unless hit by radio-wave emissionwere placed into holes made in 600x600x600mm concrete blocks. After tamping, the blocks were exposed to 1,200W microwaves at a frequency of 2.45GHz. Two minutes later the researchers saw several large monolithic pieces with few or no cracks.
With an increase in emission power cleavage time shortened and resultant fragments got smaller.
Following the experiment, the researchers claimed that the technology was relatively inexpensive, leaving little waste in the process compared to traditional blasting and helping produce higher-quality material. It could also be very helpful for other purposes, such as housebreaking, slum clearance, or rock fragmentation on construction sites.